ประวัติ Toyotismo ลักษณะขั้นตอนข้อดีและข้อเสีย
toyotismo, ระบบการผลิตของโตโยต้า (TPS) หรือการผลิตแบบลีน (การผลิตที่ไม่มีขยะ) คือ หนึ่งในสามกระบวนทัศน์หลักเกี่ยวกับระบบการผลิตซึ่งเกิดขึ้นในการตอบสนองต่อสถานการณ์เฉพาะรอบ ๆ บริษัท โตโยต้าในวัยเด็ก.
ในแง่นี้แนวคิดพื้นฐานมากมายของมันนั้นเก่าและไม่เหมือนใครกับโตโยต้า คนอื่นมีรากฐานในแหล่งดั้งเดิมมากกว่า สิ่งเหล่านี้ถูกนำมาใช้เป็นแนวทางปฏิบัติที่ดีที่สุดในอุตสาหกรรมอื่น ๆ อีกมากมายนอกเหนือจากการผลิตยานยนต์.
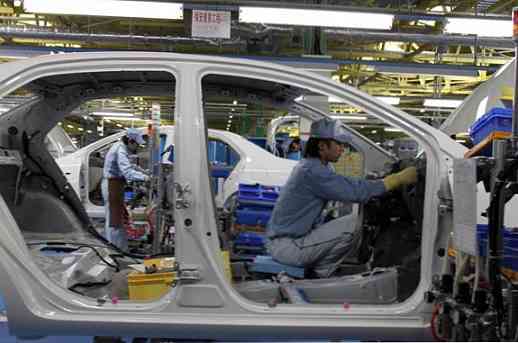
ระบบการผลิตของโตโยต้าส่วนใหญ่จะใช้ใน บริษัท ขนาดใหญ่ที่มีความเข้มข้นในการผลิตจำนวนมาก คุณสมบัติที่โดดเด่นของมันคือการจัดการขยะ (การจัดการแบบลีน) และการผลิตแบบไม่มีขยะ (การผลิตแบบลีน).
ในปี 1990 การศึกษาที่รู้จักกันดีดำเนินการโดยสถาบันเทคโนโลยีแมสซาชูเซตส์จัดตั้งปัจจัยความสำเร็จของโตโยต้า เหล่านี้คือความเป็นผู้นำด้านเทคโนโลยีความเป็นผู้นำด้านต้นทุนและความเป็นผู้นำด้านเวลา.
แนวทางขององค์กรและกลยุทธ์พื้นฐานของ บริษัท ถือว่าโรงงานเป็นระบบที่สมบูรณ์ นั่นคือระบบงานที่ซ้อนทับแต่ละสถานีงานและเวิร์กช็อป.
ดัชนี
- 1 ประวัติ
- 2 ลักษณะของ toyotismo
- 3 ขั้นตอน
- 3.1 การออกแบบระบบการผลิตที่เรียบง่าย
- 3.2 การระบุช่องว่างสำหรับการปรับปรุง
- 3.3 การปรับปรุงอย่างต่อเนื่อง
- 4 ข้อดี
- 4.1 ลดขยะ
- 4.2 มองหาประสิทธิภาพ
- 4.3 ลดต้นทุน
- 5 ข้อเสีย
- 5.1 มีความจำเป็นต้องประเมินการปรับปรุง
- 5.2 ทำงานได้ดีขึ้นด้วยส่วนประกอบที่เสถียร
- 6 ตัวอย่าง บริษัท ที่ใช้ Toyotismo
- 7 อ้างอิง
ประวัติศาสตร์
ในปี 1902 Sakichi Toyoda คิดค้นเครื่องทอผ้าที่หยุดโดยอัตโนมัติเมื่อใดก็ตามที่เขาตรวจพบว่าด้ายแตก สิ่งนี้ทำให้ไม่สามารถสร้างวัสดุที่มีข้อบกพร่องได้.
ต่อมาในปี 1924 เขาสร้างเครื่องทอผ้าอัตโนมัติที่อนุญาตให้บุคคลใช้งานหลายเครื่อง นี่คือต้นกำเนิดของหนึ่งในแนวคิดของ Toyotism: jidoka แนวคิดนี้เกี่ยวข้องกับคุณภาพในกระบวนการผลิตและการแยกคนและเครื่องจักรสำหรับการจัดการหลายกระบวนการ.
จากนั้นซากิก็สร้าง บริษัท ยานยนต์ที่เหลืออยู่ในความดูแลของคิอิชิโระโทโยดะลูกชายของเขา ในปี 1937 Kiichiro ได้สร้างวลีขึ้นมาทันเวลา (ทันเวลา).
เนื่องจากขาดเงินทุนเพียงพอ บริษัท จึงไม่สามารถเสียเงินกับอุปกรณ์หรือวัสดุส่วนเกินในการผลิต ทุกอย่างต้องตรงเวลาไม่เร็วเกินไปหรือช้าเกินไป นี่เป็นกฎที่สำคัญที่สุดลำดับที่สองของ Toyotism.
หลังจากสงครามโลกครั้งที่สองวิศวกร Taiichi Ohno ได้รับความไว้วางใจในการปรับปรุงประสิทธิภาพการทำงานและการจัดการแนวความคิดในเวลาและ jidoka เขาได้รับแต่งตั้งให้เป็นผู้จัดการร้านขายเครื่องจักรของโรงงานผลิตเครื่องยนต์และได้ทดลองกับแนวคิดมากมายในการผลิตระหว่างปี พ.ศ. 2488-2498.
งานและความพยายามของเขาส่วนใหญ่เป็นสิ่งที่ส่งผลให้เกิดการกำหนดสิ่งที่เรียกว่าระบบการผลิตของโตโยต้า.
ลักษณะของโตโยต้า
หนึ่งในคุณสมบัติของ Toyotism คือการผลิตล็อตเล็ก ๆ ปริมาณงานที่ทำในแต่ละขั้นตอนของกระบวนการกำหนดโดยความต้องการใช้วัสดุของขั้นตอนถัดไปทันทีเท่านั้น สิ่งนี้ช่วยลดต้นทุนการบำรุงรักษาสินค้าคงคลังและเวลาส่งมอบ.
ในทางตรงกันข้ามคนงานได้รับการฝึกฝนในทีม แต่ละทีมมีความรับผิดชอบและการฝึกอบรมเพื่อทำงานพิเศษหลายอย่าง.
พวกเขายังดำเนินการทำความสะอาดและซ่อมแซมอุปกรณ์เล็กน้อย แต่ละทีมมีผู้นำที่ทำงานเป็นหนึ่งในพวกเขาในบรรทัด.
นอกจากนี้คนงานจะต้องค้นหาและแก้ไขข้อบกพร่องในผลิตภัณฑ์โดยเร็วที่สุด หากไม่สามารถซ่อมแซมข้อบกพร่องได้ง่ายผู้ปฏิบัติงานใด ๆ สามารถหยุดสายทั้งเส้นได้โดยการดึงสายเคเบิล.
ในที่สุดซัพพลายเออร์จะได้รับการปฏิบัติในฐานะหุ้นส่วน สิ่งเหล่านี้ได้รับการฝึกอบรมเพื่อลดเวลาการจัดเตรียมสินค้าคงเหลือข้อบกพร่องการแยกเครื่องจักรและอื่น ๆ.
ขั้นตอน
ออกแบบระบบการผลิตที่เรียบง่าย
การไหลของระบบการผลิตไม่ควรขัดจังหวะ สามารถทำได้เมื่อมีการไหลของวัตถุดิบไปยังผลิตภัณฑ์สำเร็จรูปอย่างรวดเร็ว.
คน (ผู้ปฏิบัติงาน) และเครื่องจักร (อุปกรณ์) จะต้องมีความสมดุลอย่างเป็นระบบตามความต้องการของลูกค้า.
การระบุช่องว่างสำหรับการปรับปรุง
เป้าหมายสูงสุดคือระบบที่มีการไหลของวัสดุที่สม่ำเสมอในขณะที่เพิ่มกิจกรรมที่มีมูลค่าเพิ่มของผู้ประกอบการ.
การปรับปรุงอย่างต่อเนื่อง
ลักษณะสำคัญของ Toyotism คือการมีความยืดหยุ่นของอุปกรณ์และความสามารถในการปรับให้เข้ากับความยืดหยุ่นของผลิตภัณฑ์ สิ่งนี้จะช่วยให้สามารถตอบสนองความต้องการของลูกค้าได้อย่างรวดเร็วและในเวลาเดียวกันก็เป็นผู้ผลิตแบบทันเวลา.
ประโยชน์
ลดปริมาณขยะ
ข้อดีอย่างหนึ่งของ Toyotism คือการพยายามลดของเสียทุกรูปแบบ ซึ่งรวมถึงทุกอย่างตั้งแต่ข้อบกพร่องของวัสดุจนถึงการยศาสตร์.
มองหาประสิทธิภาพ
หลีกเลี่ยงสภาพแวดล้อมที่เป็นอุปสรรคต่อประสิทธิภาพของแรงงาน พนักงานมีส่วนร่วมอย่างแข็งขันในกระบวนการปรับปรุง สิ่งนี้ตอกย้ำความรู้สึกเป็นเจ้าของและเพิ่มแรงจูงใจ.
ลดต้นทุน
ในทางกลับกันกลยุทธ์แบบทันเวลาช่วยให้สามารถใช้ทรัพยากรของ บริษัท ได้ดีขึ้น นอกจากนี้ยังช่วยเพิ่มกระแสเงินสด ความต้องการในการจัดเก็บข้อมูลลดลงซึ่งช่วยลดต้นทุน.
พื้นที่ที่บันทึกในหน่วยเก็บสามารถใช้เพิ่มสายผลิตภัณฑ์ใหม่ได้ และพนักงานมีเวลามากขึ้นในการตอบสนองอย่างรวดเร็วต่อการเปลี่ยนแปลงความต้องการของลูกค้า.
ข้อเสีย
จำเป็นต้องให้ความสำคัญกับการปรับปรุง
การตรวจสอบผลผลิตและของเสียมีผลต่อเวลาที่ใช้ในการผลิต ต้องตรวจสอบมูลค่าของการปรับปรุง หากประสิทธิภาพในส่วนนั้นจัดการได้ดีกว่าระดับก่อนหน้านี้ผลลัพธ์จะไม่ได้รับการปรับปรุง.
ทำงานได้ดีที่สุดกับส่วนประกอบที่มั่นคง
ข้อเสียเปรียบอีกประการหนึ่งก็คือหลักการแบบทันเวลาพอดีกับส่วนประกอบที่มีเสถียรภาพของระบบ ข้อ จำกัด ใด ๆ ที่ไม่ได้คำนึงถึงในการวางแผนอาจเป็นอันตรายต่อระบบทั้งหมด.
ตัวอย่างของ บริษัท ที่ใช้ Toyotism
ตัวอย่างคลาสสิคของ บริษัท ที่ใช้ระบบนี้คือ บริษัท โตโยต้า ปรัชญาของโตโยต้าทำให้ บริษัท นี้เป็นหนึ่งใน บริษัท ยานยนต์ที่สำคัญที่สุดทั่วโลก แนวคิดนี้ได้รับการทำซ้ำทั่วโลก.
หนึ่งใน บริษัท ที่ใช้กลยุทธ์ Toyotism คือ John Deere ผู้ผลิตเครื่องจักรกลการเกษตรนี้ลงทุนอย่างมีนัยสำคัญในการเปลี่ยนการดำเนินงานในไอโอวาสหรัฐอเมริกาในปี 2003.
การปฏิบัติเหล่านี้ทำให้เขาสามารถระบุกิจกรรมได้โดยไม่ต้องเพิ่มมูลค่าและกำจัดพวกเขาเท่าที่จะทำได้.
การอ้างอิง
- Haak, R. (2003) ทฤษฎีและการจัดการของกลยุทธ์ส่วนรวมในธุรกิจระหว่างประเทศ: ผลกระทบของโลกาภิวัตน์ต่อความร่วมมือทางธุรกิจของญี่ปุ่นเยอรมันในเอเชีย. นิวยอร์ก: พัลเกรฟมักมิลลัน.
- ศิลปะแห่งการผลิตแบบลีน (s / f) คู่มือพื้นฐานของระบบการผลิตของโตโยต้า สืบค้น 7 กุมภาพันธ์ 2018 จาก artoflean.com.
- 1,000 กิจการ (s / f) 7 หลักการของระบบการผลิตของโตโยต้า (TPS) สืบค้นเมื่อวันที่ 7 กุมภาพันธ์ 2018 จาก 1000ventures.com.
- Shpak, S. (s / f) ข้อดี & ข้อเสียของการผลิตแบบลีน สืบค้นเมื่อวันที่ 7 กุมภาพันธ์ 2018 จาก smallbusiness.chron.com.
- Basak, D.; Haider, T. และ Shrivastava, A. K. (2013) ขั้นตอนเชิงกลยุทธ์เพื่อให้บรรลุระบบการผลิตแบบลีนในการจัดการการดำเนินงานที่ทันสมัย วารสารวิทยาศาสตร์คอมพิวเตอร์และการจัดการระหว่างประเทศ, การศึกษาปีที่ 13, ฉบับที่ 5, pp. 14-17.
- การผลิตทั่วโลก (2014, 11 มิถุนายน) 10 อันดับแรก: บริษัท ผลิตแบบลีนในโลก สืบค้นเมื่อวันที่ 7 กุมภาพันธ์ 2018 จาก manufacturingglobal.com.